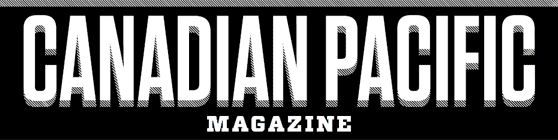
Vol 29 - 2021
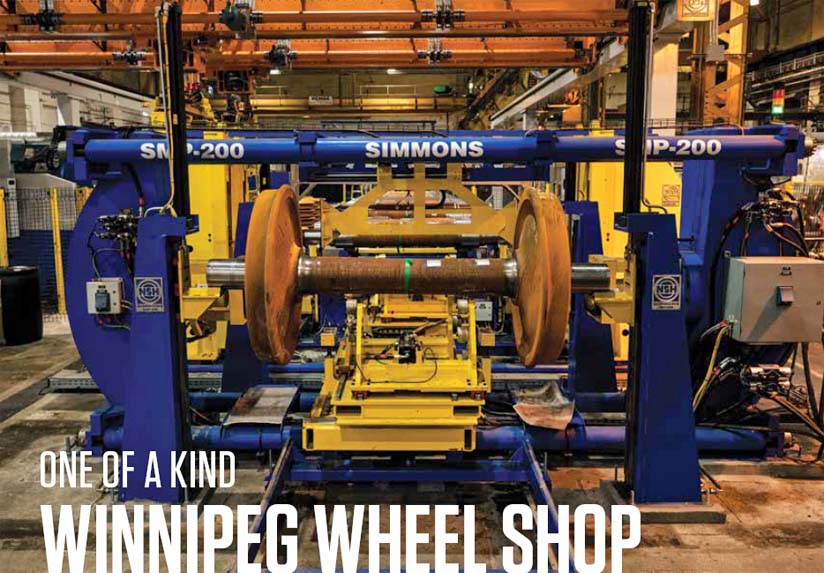
The Winnipeg Wheel Shop has undergone a technological transformation during the past three years. Once an outdated production facility, it is
now a leading example of innovating to create new high-value and safer work for CP and our employees.
Part of several different shops housed in the cavernous main facility that is Weston Shops, the wheel shop supports CP's business by providing economical in-house solutions to costly activities. Workers produce the wheelsets that CP's equipment runs on, and then ships them to shops across the system. Performing this type of work in-house saves the company millions of dollars in third party contracts. It enables CP to control costs while optimizing our assets.
Built in 1972, the wheel shop employs about 60 people and produces more than 35,000 wheelsets for CP's carshops. In recent years, some of the shop's equipment had become outdated or was approaching the end of its useful life.
"The new wheel shop will automate formerly manual processes so we can operate even more safely and move our skilled employees' efforts to higher-value tasks," said Rui Botelho, Director Weston Production Facility, of which the wheel shop is a part.
"We'll also generate new performance data on wheel production cycle time, quality, and cost, which will help us better predict future production
needs. Ultimately, this will all help us move our customers' shipments more efficiently and reliably."
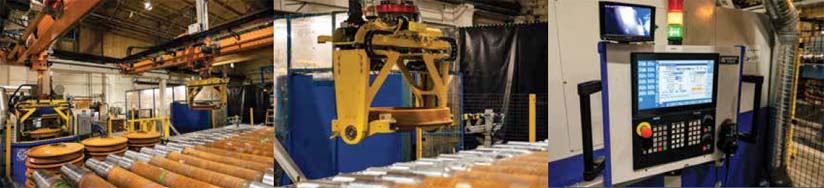
The Weston Production Facility is one of a kind. As one of the only Class 1 railways to produce its own wheels and track components internally,
CP benefits from not needing to source a significant portion of our material from outside suppliers.
"Unlike third parties, we have a zero-based cost model," said Botelho. "CP saves money, e aren't working with profit margins and are much more competitive from a cost perspective."
The wheel shop is a beacon of innovation where robotic technology is slowly being introduced to streamline and ultimately increase wheel production. This four-phase, multi-year, approach will replace the functional areas of the existing wheel shop with new, modern, technologies, all inside the existing footprint of the shop. On the outside, the building looks the same as it always has. On the inside, everything is undergoing change.
"Our wheel shop redesign started with the ambitious goal of building the rail industry's most innovative wheel shop. In 2017, we underwent a search for the cutting-edge technologies that would help us not only produce more wheels more efficiently, but more safely," Botelho said.
The first two phases of the facility upgrade are complete, with the final two phases set to be reviewed and scoped during the next few years. Phase one, completed in 2019, featured the installation of a robotic bearing mount. A series of strategically placed cameras locate the wheel bearings on pallets, and the robotic arm then picks them off the conveyor belt and moves them into place for production.
"This reduction in manual handling of the bearings, which often used to be done three to four times or more per shift, means a safer work
environment for our employees and a faster, more efficient way to prepare the bearings for installation on freight car wheelsets," said
Botelho.
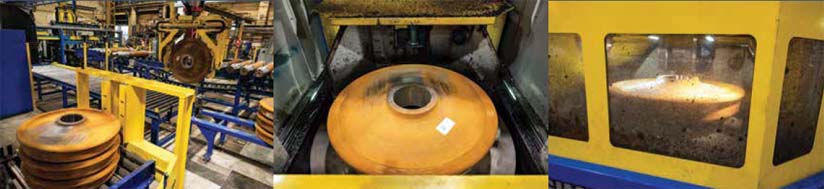
In the second phase of the redesign project, completed in six weeks in 2021, we further enhanced our ability to produce outgoing wheelsets by
adding machining and mounting press operations. The automated system measures the axle and machines the inside portion of the wheel (wheel blank) to
ensure that the two pieces fit together, then presses them. The automated system makes sure that the two components have precise measurements to reduce
rework.
"These first two phases have already increased our production capacity by 40 percent," Botelho said.
The final two phases incorporate technologies that will streamline axle processing and machining, and the intake of wheels as they first come into
the facility from the field for inspection and refurbishment. By the time we're done with the redesign, our highly trained employees at the Winnipeg
Wheel Shop will be making 95 percent of all our wheels using state-of-the-art technologies that are unmatched across the rail
industry.
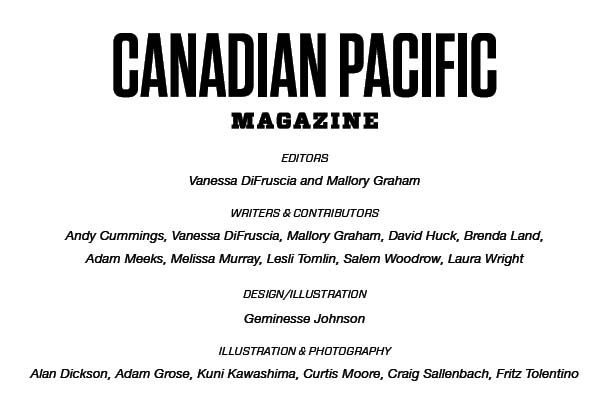
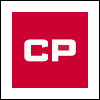