Issue 2
September 2003
 Canadian Pacific
Railway Employee Communications Room 500 401-9th Ave S.W. Calgary AB
T2P 4Z4
FOCUS ON
FUEL Dave Jones
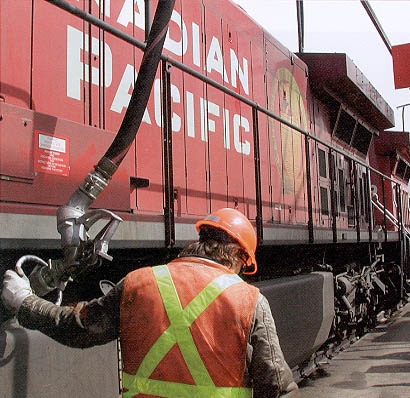 CPR's fuel consumption has dropped 20
percent in recent years, largely as a result of new, more efficient locomotives, but
also through a multi-faceted approach to conservation.
New conservation
techniques and technologies could save million of dollars at the pump
In railroading, fuel costs are second only to labor. Diligent train handling, price
hedging and a little luck can mean the difference between a poor balance sheet and
financial success. Left to the uncertainty of the marketplace, for every dollar the
price of a barrel rises ( based on the market price of West Texas crude ), our bottom
line takes about a $10 million Cdn hit.
In North America, locomotive fuel consumption is measured by calculating the number of
US gallons it takes to haul 1,000 gross tons one mile. In Canada, we also calculate it
by litres per 1,000 gross ton miles. Many strategies are used to improve that number,
from reducing train speeds and employing strict shutdown guidelines when idling or not
moving, to monitoring train handling techniques for best practices. Over the last
five years, fuel consumption at CPR has dropped 20 percent, largely as a result of
replacing one-third of our locomotive fleet with new, more fuel efficient
units, but also from a multi-faceted approach to fuel conservation.
Our goal this year is to reduce our current 1.244 gallons ( 4.71 litres ) per 1,000
gross ton miles - the third best rate among North American Class 1 railroads - to
about 1.228 gallons ( 4.65 litres ).
"Much of our effort to date has been with automated start and shutdown
systems", said John Anderson, CPR manager of locomotive fuel conservation.
"We have 1,585 locomotives operating on our system and they spend up to 50
percent of their time idling, each burning about 2.7 gallons an hour. When you do the
math, there's a potential savings of about $20 million. We are continually modifying
and equipping our locomotives with this technology as our engines come in for regular
or unscheduled maintenance.
|
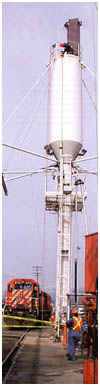 Fuel efficiency depends on
using the proper procedures at filling stations, employing good train handling
techniques, and observing strict shutdown guidelines.
|
Nearly half of the CPR fleet, or 751 units, are equipped with one form of auto
shutdown or another. Three systems - ZTR Smartstart, QEG Electronic Governor, and GE
AESS ( Auto Engine StopStart ) - are operating on everything from yard engines and
switchers to our big AC traction road engines. All are designed to shutdown and start
up locomotives, as necessary, to maintain not only engine temperature, but battery
voltage and brake pressure. In addition, a device designed by EcoTrans is being tested
by several railroads, including CPR, to keep engine oil and water warm while the
locomotives are shut down. EcoTrans states that units equipped with their innovative
technology use about one-tenth the fuel of idling locomotives.
"Currently, CPR fuel management is working in conjunction with our systems
development & planning people on the automated analysis of locomotive event
recorders", John said. "From the event recorder download, road managers
will be able to identify how well trains are being handled over their respective
territory and how compliant to our fuel conservation policy they are for each
individual trip. Locomotive engineers will be notified in a timely manner about the
results of the download and how they were graded. The data will be housed in a
confidential database to be used when information is requested by regulatory bodies,
or when we want to keep tabs on individual performance. We can also use the data to
recognize top performers and help to identify potential management candidates".
The analysis will also identify exceptions to permissible train speed, track speed,
slow order speed, and other considerations. This will promote safety and should
result in a reduction in train accidents and cardinal rules violations. It also
supports the transportation/field operations safety plan by managing risks and safety
failures, ensuring compliance and supporting recognition and feedback.
Some railroads are already experimenting with sending event recorder data directly to
their mainframe computers through the use of wireless technology and radio downloads.
This gives fuel and road managers the ability to make quick decisions and identify
appropriate training needs.
And, of course, as governments on both sides of the border introduce tougher emissions
controls, no strategy or locomotive component can afford to go unexamined. Research in
the US is developing bearings that reduce drag, hybrid
diesel/battery-powered locomotives, more efficient fuel injectors and
new lubrications to reduce wheel and rail wear.
"When you're talking about consuming tens of millions of gallons of fuel every
year", John said, "you have to look at every kind of fuel-saving
technology at your disposal. And, more importantly, you have to have every one of your
train and yard crew members, rail traffic controllers, mechanical and engineering
services employees as a committed conservationist.
"Success usually comes to those who are too busy looking for it. Lets all get
busy".
©
2005 William C. Slim
http://www.okthepk.ca
|