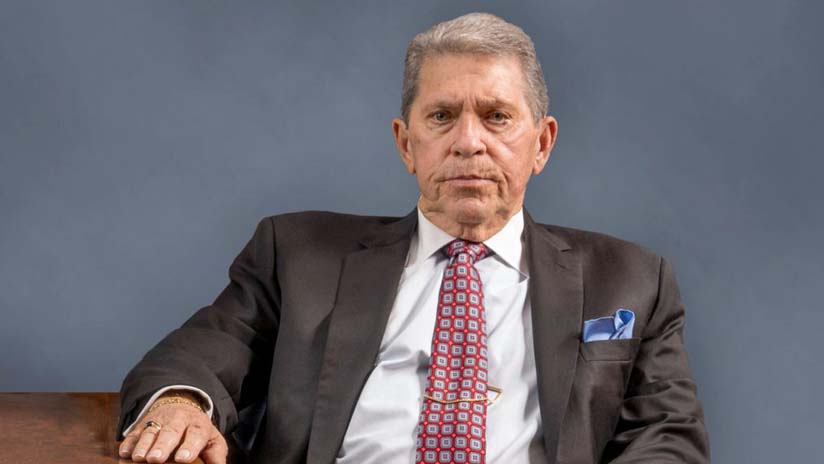
North America - "It's time to run another train east."
These are the exact words I used when working for the Southern Pacific Railroad (SP) as an Assistant Terminal Superintendent at the Roseville, California,
terminal in 1969.
This was "smart railroading" for most railroads in the 20th Century.
Now, Precision Scheduled Railroading (PSR) governs operating decisions on most railroads.
What was this "old way?"
Why is PSR the "go to" management tool for today's rail operations?
This writing hopes to give the reader a better understanding of the light-year change in the railroad operation decision making process, all to benefit the
shipper, railroad management, employees, and the investors.
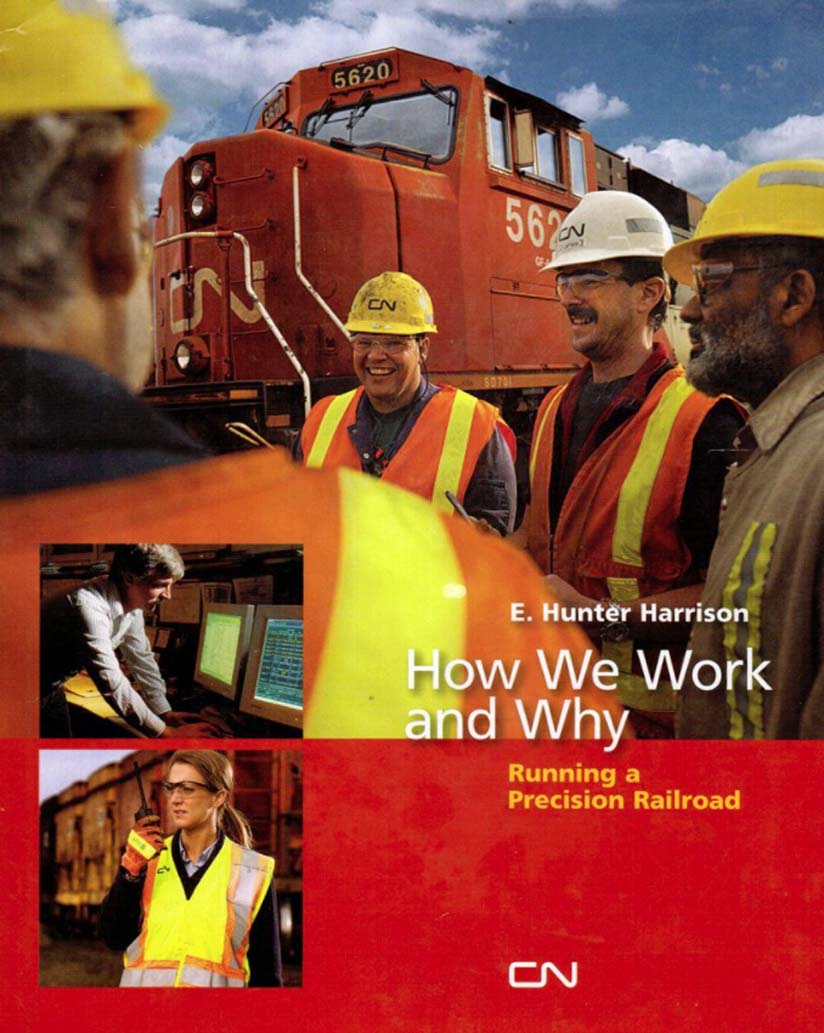
Much literature and pundit column writing covers PSR, both with a positive and negative perspective.
PSR began with Hunter Harrison making operating changes on the Illinois Central Gulf Railroad (ICG), then later on CN.
That followed several years later with his applying the same philosophy to the Canadian Pacific, and most recently with CSX.
However, there is very little literature that best explains both the previous operational decision-making process, and how PSR has revolutionized
everything.
Even the shipping customers in many cases do not understand the long-term benefits.
They only reported the chaos that ensued during the conversion to the new process.
Even the "Bible" of PSR, How We Work and Why, written by Hunter Harrison, is now out of print.
Yet, the real story must be told so all interested and affected parties today really understand how PSR has revolutionized the industry.
The key word is "Schedule."
Back in the mid-1960s and deep into the 1980s, the goal of "smart railroading" was to maximize efficiencies by operating longer, heavier trains so as
to reduce the crew cost per car handled.
Many railroads still operated with five-man crews and cabooses.
This "large train" maxim was almost totally dictated by decisions made at each yard terminal where cars were accumulated.
For SP, the Roseville Terminal with its twin hump yard gathered revenue cars from Northern California, the San Francisco Bay Area, the Central Valley of
California, and especially the perishable traffic from the Salinas Valley of California.
As a Terminal Manager, every morning at 06:00 we built our "Game Plan" for the next 24 hours.
To create the plan, the underlying axiom was to build large trains so as to maximize train crew utilization.
Also, it reduced the total number of trains on the main line so as to make the route more fluid.
Commodity type, such as reefers carrying perishables, also dictated priority for assigning cars to the first train to be sent east over the old Central Pacific
original route.
This we called Step 1.
Did it work?
SP in 1965 boasted handling the highest GTMs (Gross Ton-Miles) per track-mile of any of the Class I railroads, almost double the next best
railroad.
Almost all railroads were operated by actions dictated by the various terminals.
Only locals, mostly branch line "single train a day" locals, had a predetermined schedule.
After Step 1, the decision that passed the "large enough" number of cars test, came Step 2, assigning a train schedule.
SP had numerous schedules that could be assigned to a potential train, such as RSVNPT23.
This indicated a Roseville (RSV) originating train for destinations on the Union Pacific North Platte, Nebraska, terminal (NPT) and beyond, set to depart on
day number 23 of the month.
Then came Step 3, the marshaling of resources.
Are there sufficient locomotives?
Is there a rested crew?
Finally, Step 4 closed the decision loop by assuring all the cars selected to be on this train were switched out and ready to be placed on the new
train.
As part of this process, one would make a sweep of the car inventory of the terminal to spot any "hot cars" that had been badly delayed, or cars
recently released from the Repair Track and ready to be put back in circulation.
Now came the decision time to "Call the RSVNPT23 for 11:00."
All that remained was execution.
The switch crews had to build the train, the roundhouse had to select, inspect, test, and fuel the locomotives, and move the power to the departing train's
track.
Meanwhile, the mechanical department had to lace up the air hoses and make an Initial Terminal Air Brake Test.
Last of all, the train crew, one that had been called for duty 90 minutes before the scheduled departure, was delivered to the train.
At the end of this process, the train crew received the "green light" indicating the train was ready to depart and the route was lined for
movement.
Note, in this decision scenario, no factor was introduced that recognized that both the locomotives and train crews eventually had to make a return move to
balance resources.
The decision was always a "one-way" decision in which the return of assets fell to future train movements from other terminals, eventually bringing
assets back to their origin.
So what changed?
What did PSR do to make this the "new way to railroad?"
Note the wording above that says "scheduled train."
That was a very accurate statement, and became the source of most management performance reviews.
However, what was the "car schedule?"
If the carload came off a branch line or shortline with once-a-day service, the shipper usually could anticipate the time of day that the car would be pulled
from the loading dock by the local.
It "left on schedule."
However, once that car reached a terminal or interchange track, it became co-mingled with many other cars, and totally lost its schedule
identity.
The only time clock that was acknowledged to occur was when there was a sweep of the car inventory in the terminal to spot any cars having not moved in the
past 24 or 36 hours.
As mentioned in Step 4, delayed cars might become part of the next train.
At this period in railroading, all Class I railroads made weekly reports to the Association of American Railroads that showed "terminal dwell
time."
It consistently averaged well over 24 hours.
Some railroads tried to reduce that average by including trains that only changed crews or locomotives, but otherwise were "run through" trains, but
the average dwell time told the story.
Only CN consistently reported dwell times under 20 hours.
This was well under the 24 hour average.
At that same time, CN was the only Class I railroad reporting an Operating Ratio at least 10 points lower (better) than its competitors.
Here in lays the base for the success of PSR: Operating Ratio is the Revenue divided by the Expenses for the railroad.
When a railroad changes from a "train schedule" to a true "car schedule," the railroad industry starts to talk like a truck
driver.
That trucker will tell their customer the exact time the load will reach destination.
The loaded trailer never stops, except for fueling, food, and rest, all scheduled by the driver.
For a PSR railroad, the same type anticipated schedule can be built, combining advanced train schedules for the rail car to connect to each next scheduled
train along the route.
That time the local train picked up the new loaded car becomes the basis upon which the schedule for the whole trip becomes the basis for
performance.
It becomes the railroad's measured and committed obligation to deliver the car "on schedule."
Once the shipper realizes the benefits of PSR, they find they can plan their loading (or unloading) work schedule more efficiently, and avoid the bunching of
cars that often leads to demurrage charges.
My company, RailTex, had four of our 24 Class III railroads connected with CN.
New customer sales success was much easier to achieve with the CN connections than with our other primary interchanges with CSX, Union Pacific, and Norfolk
Southern.
The shipper using CN long-haul loved PSR.
Where does the railroad that practices PSR achieve the benefits?
How can you possibly make more of a profit if the schedule calls for a certain train schedule connection, and only 50 cars are available to fill the train to
meet the scheduled departure time?
The answer relates to that old Army axiom, "Poor Prior Planning Produces Poor Performance."
Before PSR, the Step 1 (see above) to run a train when there are 100 cars never factored in the return of the locomotives or crews back home for the next
100 car train.
It was assumed there would be traffic moving in the opposite direction that allowed repositioning the crews and power back home.
That did happen, eventually, but there were many "penalty costs" associated with the lack of prior planning to balance resources.
Crews would be "deadheaded home" to avoid "Held Away From Home Terminal" penalty pay.
Often, locomotives would be moved back in the opposite direction as "cab hops" with only power and crews, but no rail cars in the created
"train."
Under PSR, once a crew is rested, there should be another train coming in the opposite direction to balance crews.
Deadheading is eliminated.
The Held Away penalty is eliminated.
On the ICG, Hunter Harrison even reorganized crew districts so crews would swap trains midway in the crew district, and be back home within the 12 Hours of
Service Law.
This eliminated all lodging costs for hotel and food expenses.
Another benefit of PSR is the improvement of terminal fluidity, where congestion from train bunching causes some arriving trains to be "held out" of
the terminal.
Often that "held out" train had the train crew "die" under the 12 Hours of Service Law.
This resulted in another crew being called to "Dog Catch" the held-out train.
This new crew often had to move the train only the last 10-20 miles, yet received a full day's pay.
There was the taxi cost, too, to exchange crews.
PSR eliminates most, if not all, "non-productive" costs.
That situation greatly affects the expense side of the Operating Ratio.
It is not cost "reduction."
It is cost "elimination."
Consider the benefits of balancing locomotives by scheduling their assignments.
Some railroads completely eliminated the Locomotive Service Bureau function because of PSR.
No longer will one find locomotives idling in remote areas.
There is no need "to accumulate power" in anticipation of the demands over the next 24 hours.
As recently as this past Fall, railroads showed they had 4,000 locomotives in storage.
Yes, business might have slowed, but PSR has contributed to a significant improvement in locomotive utilization.
From another perspective, consider the track capacity utilization before and after PSR.
When most dwell times for cars averaged well over 24 hours, it told the situation of revenue cars sitting for more than a day, and often at more than one
terminal along their journey.
Dick Spence, SP Vice President for Operations, once lectured me when "inspecting" my rail yard filled with cars from interchange in New
Orleans.
I was the Terminal Superintendent.
"Bruce, what I see here are revenue loads the customer is paying us to move, not to sit still."
PSR is the answer.
Move cars that have their own schedule for connecting trains.
That delayed car occupies 50 feet or more of track.
Operating terminals are not storage yards.
Yet the dwell time data shows the true situation of delayed revenue loads.
Now, realize there is another benefit of PSR, safety.
As a Division Superintendent, one of my greatest fears was a train crew falling asleep when operating a train.
The most common accident involving a sleeping crew occurs when a train is diverted into a siding on a CTC-controlled route and not stopping between switches to
meet an opposing train.
A collision occurs.
Because of sleep deprivation, the crew does not respond to red signal indications.
Positive Train Control (PTC) will address most of these types of potential accidents, but it is still important to recognize this sleep deprivation
situation.
An accident investigation will show "crew sleeping" as the cause.
However, the root cause is something entirely different.
Disturbingly often, the root cause occurred back when the sleeping crew was returning home after a run, and was signing off duty around 10:00.
When asking the dispatcher or crew caller when the crew would next be expecting to be called to staff another train, the answer would be, "There is
nothing to be called for you until at least tomorrow morning after 07:00."
As a result, our employee saw that daylight time as free, and still got 8 hours rest in the evening before being called to work again.
The persons might play golf, garden, or paint the house.
This was a responsible, dedicated employee trying to properly manage their rest cycle before having to return to work.
However, because of "unforeseen operating conditions," that employee was called back to work at 23:00 just as the sleep cycle was
beginning.
Realize, under the Hours of Service Law, the employee is considered fully rested.
The condition of sleep deprivation catches up with the employee after several hours back on duty.
Under a PSR scenario, there is no need for "short-rested" calls back to work because of "unforeseen operating conditions."
Recall, Poor Prior Planning Produces Poor Performance, even in the area of safety.
PSR can easily take the blame from shippers, investors, and "rail experts" who express the many negative occurrences when converting to
PSR.
Execution, when not done in a decisive manner, and not fully understood by all parties, can cause major distress for everyone.
However, once implemented, PSR is a "win-win" for everyone:
1. The shipper - The party that pays the freight cost receives a trucker style transit schedule:
- This allows more accurate planning at the loading and unloading dock.
- Cars have the potential to arrive without bunching situations, which can lead to the penalty payment of demurrage charges.
- The freight rate will be much lower than the truck cost, even with a slightly longer transit time.
2. The train crew - There are multiple cost eliminations making for a better work experience:
- No Held Away from Home Terminal penalty payment by railroad;
- No non-productive deadheading payments to balance crews;
- For many situations, no away from home situations by trading train crews enroute;
- No "short rested" calls to return to work improves safety;
- No situations where their train is close to the terminal, but held out due to congestion in the terminal.
3. Yard Terminal operators - PSR has proven to reduce the average dwell time of cars in a terminal which shows these benefits:
- More unused track capacity;
- More efficient use of the Mechanical Department employees by better matching crews to scheduled arriving and departing trains;
- No "held out" trains due to congestion in the terminal from a bunching of train arrivals, so eliminating "dog catching" expenses to bring the held out train the last 10-20 miles, including eliminating taxis;
- Not having to worry about adequate motive power for the next train;
- No rested crew issues to staff the next train.
4. Operating Ratio Improvements - by increasing the ratio top line revenue and reducing the ratio bottom line number by lowering expenses:
- Eliminating expenses, not just lowering expenses, by avoiding nonproductive costs, such as deadheading crews, cab hops and "Dog Catching" trains held out of terminals;
- Eliminating Held Away From Home Terminal penalty expense;
- Reducing and often eliminating Away from Home hotel and food expenses;
- Increasing revenue due to shippers having the confidence of a "trucker like" scheduled transit time, so they will ship more by rail than truck. Shippers like PSR;
- Investors in railroad stocks: Increase the market value of the publicly traded stock. Just ask investors in CSX or CP stock. More profits for a PSR operator. More revenue due to satisfied shippers.
There are significant reasons that PSR has become the 21st Century way of railroading.
However, for a railroad to convert to this new paradigm, there must be Perfect Execution.
That is a management challenge, often difficult to execute.
Second, shippers, especially prospective new customers, must be educated to the benefits of PSR.
Railroads practicing PSR are offering a service just like a trucker promises, a planned total trip schedule.
However, the railroad can offer that service at a significantly lower cost than its truck competition.
Everyone wins with PSR.
Bruce M. Flohr.
(because there was no image with original article)
(usually because it's been seen before)
provisions in Section 29 of the Canadian
Copyright Modernization Act.